Neodymium Motor Magnets
Motor Magnets
Motor Magnets, Motor Permanent Magnets, Magnets for Motor Applications, Permanent Motor Magnets, Permanent Magnets for Motors, Generators, and Actuators Application
Motor Magnets: Magnets and assemblies from UPMAG can be found in many types of motors, generators, and actuators.
Rare Earth magnets (Samarium Cobalt and Neodymium), or Ferrite (Ceramic) magnets can be used in magnetic motor and vehicle magnet applications. Rare Earth magnets are typically two to three times stronger than ferrite or ceramic permanent magnets. In electric motors, that results in greater performance from smaller, lighter motors. However, rare earth magnets are also more expensive than ferrite (ceramic) options.
Motor Magnets – Magnetic technology for the motor / VCM market delivers the ability to push the limits on miniaturization, efficiency and performance. our customers wish to achieve extreme performance in devices such as a wire bonding machines and missile guidance systems. Our customers challenge us to design motors and actuators with features such as:
High force to mass ratio
High speed moving coil designs
Harsh environment withstand capability
The types of motor using permanent magnet such as :
DC motor magnets
Brushless motor magnets
Servo motor magnets
Stepper motor magnets
Linear motor magnets
PM motor magnets
Irregular motor magnets
Automobile motor magnets /Car motor magnets
High performance actuator and motor design requires the use of materials that push the limits of material science. Magnet material selection is critical and we can assist in the selection of the best material. Tradeoffs in the selection include temperature, residual induction, coercivity and environment.
Block shape of magnets with high precision, low demagnetization
&
N42SH ring magnet with multi-poles are applied to robot arms:
Neodymium Magnets used in Magnetic Motor Applications
Neodymium magnets are also used in electric car motor applications. From the motor that spins a DVD disc to the wheels of a hybrid car, neodymium magnets are used throughout the vehicle. The decision between Samarium Cobalt or Neodymium as a vehicle magnet is usually based on either operating temperature and/or corrosion resistance.
Operating temperature: A low coercivity grade Neodymium magnet may begin to lose strength if heated above 176°F (80°C). High coercivity grade Neodymium Magnets have been developed to function at temperatures up to 428°F (220°C) with little irreversible loss. The need for low temperature coefficient in neodymium magnet applications has triggered several grades to be developed to meet specific operating
requirements. Please refer to our chart of magnetic properties to compare the characteristics of each grade.
Corrosion: Neodymium magnets are vulnerable to corrosion, especially along grain boundaries of a sintered magnet. This type of corrosion can cause serious deterioration, including crumbling of a magnet into a powder of small magnetic particles. This vulnerability is addressed by adding a protective coating to prevent exposure to the atmosphere. Nickel plating or two-layered copper-nickel plating are the standard methods, although plating with other metals or polymer and lacquer protective coatings are also available.
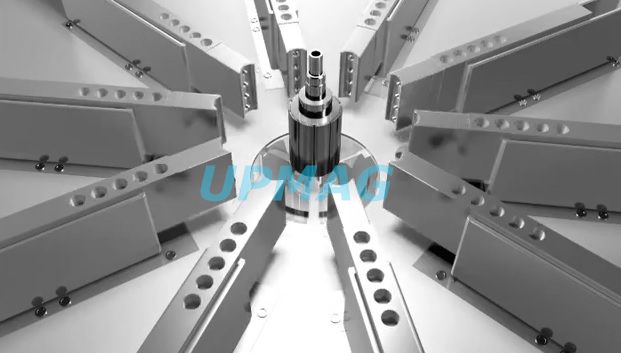
Advantages and Disadvantages of NdFeB Permanent Magnets are applied to Morots:
1) It is the strongest magnetic of permanent magnets, has the high energy (BH value) and good coercive force.
2) Manufacturing by the the vacuum sintering process, process maturity;small dimensions,have the good performances and prices; energy (BH value) of NdFeB magnets is more than ten times higher than Ferrites, it is the strongest magnetic materials in the world today, have “magnetic king”reputation.
3) Using the cutting process after sintering,according to the requirements,by the rapid processing, they can be cutted into square,disc.,ring,segment(like tile shape),and so on.
4) NdFeB permanent magnets are easy to be rusted/oxided, so their surface should be done eletroplating treatment, such as galvanized(Zn coating), Nickel+copper+nickel, and so on, generally, it requests more than 48hours in Salt-spray test; also can be passivated treament to slow down its oxidative speed.
For more details or any inquiry pls contact : info@upmagnet.com